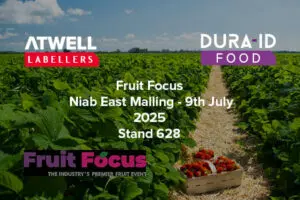
See us at Fruit Focus 2025
We are delighted to be exhibiting at Fruit Focus 2025 hosted at Niab East Malling on the 9th July 2025. Find us on stand 628...
Read Full ArticleWe are delighted to be exhibiting at Fruit Focus 2025 hosted at Niab East Malling on the 9th July 2025. Find us on stand 628...
Read Full ArticleToday, we are sharing the top things to look for when purchasing a new labelling machine.
Read Full ArticleHere are the five key types of labelling machines to help you narrow down your search:
Read Full ArticleHand labelling is a great way to get your products and business off the ground, but as your brand grows and sales increase, it can...
Read Full ArticleIf you’ve never purchased a used labelling machine before, or you’re replacing an old one, it's critical you pick a supplier you can rely on.
Read Full ArticleThese are three questions you should always ask before investing in a new bottle labelling machine:
Read Full ArticleBusinesses are wary of making the investment for an automatic labelling machine, it is important to understand the benefits they can bring.
Read Full ArticleWe’re sharing our top five unique ways to use a labelling machine for your products:
Read Full ArticleExploring how labelling machinery can help your business tackle the skills shortage and keep your production line running smoothly.
Read Full ArticleAtwell Labellers will be exhibiting at EmPack 2025 at the NEC, Birmingham, B40 1NT on the 12th and 13th of February, alongside our sister company,...
Read Full Article