Machine Servicing and Support
Why Choose Atwell Labellers Machines and Servicing?
Our team of in-house engineers are always on hand to assist you.
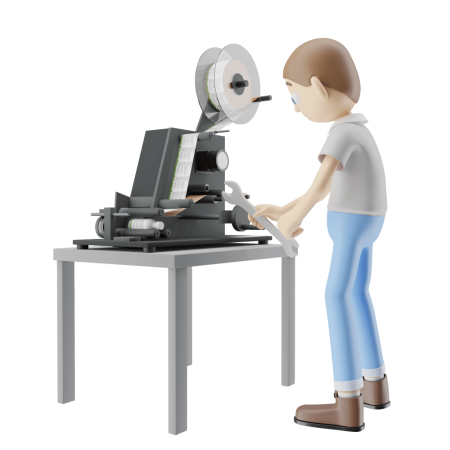
Machine Servicing & Support
Discover Our Service Plans
Peace of mind and maximum uptime – that’s what our machine servicing and service contracts are all about. We understand that a smooth-running label applicator is vital to your business, and we’re here to ensure it stays that way.
New Machines
Atwell systems are engineered to be easy to operate whilst being reliable and efficient.
Every new machine comes with a 12-month warranty: parts, labour, and even travel costs are covered (excluding accidental or wilful damage, and consumable items). Give yourself peace of mind when purchasing a machine from Atwell Labellers. When your warranty ends, we’ll get in touch about a bespoke service contract to ensure a seamless transition to regular servicing and support.
We offer comprehensive on-site training for your operators and production staff when you purchase a new machine. If your needs evolve, we also offer flexible, in-house training options throughout the machine’s life cycle, all delivered by our knowledgeable engineers.
Our dedicated Technical Helpline is manned throughout the week, giving you direct access to engineers who know your machine and can often resolve issues over the phone, saving you valuable time
Service Contracts
Our machines are simple to use, built to last, and flexible enough to grow with your business.
Tailored to your needs: We won’t offer you a one-size-fits-all contract. We listen to your specific requirements and craft a service plan that works perfectly for you. Plus, you’ll enjoy a discounted price compared to our standard call-out charge.
Whether you’re a contract holder or not, you can arrange an on-site visit from our fully-qualified engineers. Contract holders always get priority, but everyone receives the same dedication and expertise. Our engineers cover the UK, Ireland, and beyond, and their fully stocked vans are equipped for most eventualities.
Our fully stocked stores mean we’re ready to tackle breakdowns head-on. Every machine is unique, so there may be times when parts aren’t readily available, but we’ll work tirelessly to get them to you as fast as possible. We even provide a recommended spare parts list for you to store on-site, minimizing downtime.
Invest in peace of mind, invest in uptime, invest in a service contract from Atwell Labellers.
Contact us today to discuss your specific requirements and experience the difference.
Why Servicing is so Important
Regular servicing offers a slew of benefits that keep your labels perfect and your production flowing smoothly:
1. Peak Performance: Just like a well-oiled engine, a regularly serviced applicator runs smoother, faster, and more efficiently. Expect consistent label application, reduced jams and misaligned labels, and improved overall accuracy.
2. Extended Lifespan: Regular maintenance catches and resolves minor issues before they snowball into bigger problems. This not only avoids costly repairs but also extends the life of your applicator, saving you money in the long run.
3. Minimised Downtime: Breakdowns are the bane of any production line. By proactively addressing potential issues through servicing, you significantly reduce the risk of unexpected downtime, keeping your production on schedule and your customers happy.
4. Enhanced Safety: Worn parts and malfunctioning components can pose safety hazards. Regular servicing identifies these issues and ensures your applicator operates safely and reliably, protecting your employees from potential harm.
5. Optimised Costs: While you might see servicing as an expense, it’s actually an investment that saves you money in the long run. Regular maintenance prevents major breakdowns, extends the life of your applicator, and reduces downtime, all of which contribute to significant cost savings.
Frequently Asked Questions
Have a question about our services or want to know more, take a read of these questions our customers often ask.
What engineering service support cover do ATWELL provide?
Here at Atwell Labellers, we have a nationwide network of engineers located throughout the UK.
What are the benefits of taking out a service contract?
We can offer you a reduced rate for callouts compared to individual site visits, and we will always prioritise your needs.
What level of maintenance is required for any machine?
A weekly check is listed in the manual as a suggestion, but regular or annual services of the machine carried out by an Atwell engineer are crucial for optimal performance.
How do I maintain my label applicator?
We provide maintenance guides and offer servicing packages to ensure your equipment runs smoothly.
How do I arrange a service visit?
To arrange a service visit from one of our specialised engineers you have a few options. You can email or call your sales reprehensive, or contact the team on the email address or phone number below.
Can we help you?
Technical Helpline
Contact by Telephone:
+44 (0)1444 237 804
Contact by Email:
Latest News & Case Studies
Visit Us At UK Packaging 2025
See us at Fruit Focus 2025
Little’s Coffee – Improved Visibility and Security Branding with Atwell Labellers
You May Also Be Interested In
Want Us to Call You?
If you have any questions about our services or how our services could help you, ask one of our dedicated team of experts to give you a call, just fill out this handy form and we will be right with you.