Dispergo Vaping - Case Study
Objective
To increase production by automating the filling and labelling process, enabling Dispergo Vaping to meet growing demand without escalating staffing costs.
At a Glance
Challenges:
- Increasing production capacity while maintaining or improving label quality.
- Eliminating inconsistencies that arose from manual labelling processes.
- Meeting growing demand without significantly expanding the workforce.
Benefits:
- Production capacity increased from 1,000 bottles per hour to 3,500, allowing Dispergo Vaping to keep up with demand efficiently.
- Reduction in manual labour, freeing up staff for other tasks and minimising repetitive strain.
- Consistent, high-quality labelling across various bottle sizes.
Solutions
Marking its fifth year in business, Dispergo Vaping continues to innovate by creating unique e-liquids for stores nationwide. To support rapid growth, they needed a reliable, automated solution to increase output without the rising costs associated with hiring additional staff.
Manual labelling presented challenges, such as inconsistent application and delays in production. After receiving high recommendations from other customers, Dispergo chose Atwell Labellers for their solution. Atwell’s linear wrap applicator was the ideal choice, thanks to its flexibility and seamless integration with Dispergo’s existing filling machine. This automation ensured that production continued without interruption during installation.
The installed system handles various bottle sizes, from 10ml to 120ml, maintaining precision and quality regardless of the volume. With its robust capabilities, the applicator significantly increased Dispergo’s output, helping them stay ahead in a competitive market while reducing the need for manual interventions.
Results and Impact
Since implementing the automated system, Dispergo Vaping has experienced consistent, high-quality labelling that aligns with their brand’s standards. The increased production capacity has allowed the company to fulfill more orders without compromising on quality or customer satisfaction. The reduction in manual labour has also led to cost savings and allowed the workforce to focus on more strategic tasks.
Future Plans
Looking ahead, Dispergo Vaping plans to continue investing in automation to further optimize their production processes. With the successful implementation of the labelling system, they are exploring additional ways to expand their capabilities and maintain a competitive edge in the vaping industry.
Quote From Dispergo Vaping
“Their outstanding customer service and continued support have ensured a seamless integration of their solutions into our operations. From installation to ongoing maintenance, Atwell’s team has been consistently reliable, enabling us to optimise our labelling processes with confidence.”
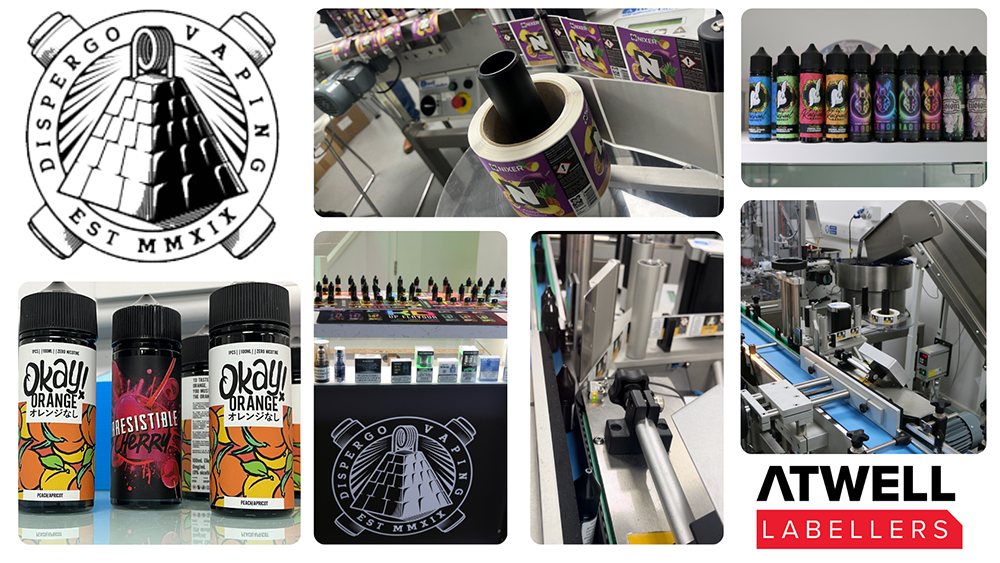